Every worker loves new technology, right? Not quite. The truth is, even in today’s business world, where certain segments seem dominated by news of an ‘always on’ culture, adopting and training on new technology can be daunting for plenty of employees. Training Employees on New Time & Attendance Software Perhaps you’ve recently added one or […]
Read More >Manufacturing Survey Results Reveal the Top Administrative Complexities Within The Warehouse
- nettime solutions staff
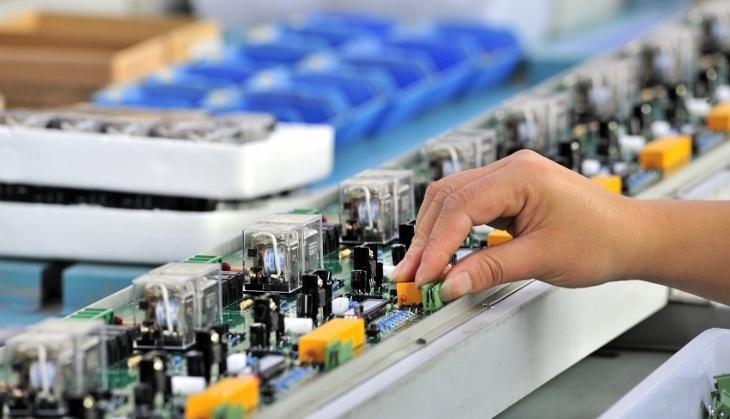
Automation is key when it comes to maintaining a successful workflow within a Manufacturing environment. Unfortunately, automation isn’t consistently implemented for all processes across the warehouse.
As a result, bottlenecks can occur and labor productivity levels are negatively affected. During a recent survey, which we conducted, the main contributors to administrative complexities were related to: reporting incidents and attendance.
Reporting Incidents
Manually tracking incidents in the workplace, and accurately reporting them takes time. In a recent survey, 79% of the participants reported that 10-20 incidents occur within their warehouse, on average, each month.
If each and every one of the incidences isn’t handled appropriately, the risk of an error occurring can escalate, especially if it’s a manual process. 73% stated they had to manually relay their incident to the company’s HR department.
Having an automated system to keep you and your team within compliance guidelines is a great way to reduce risk and avoid year-end accounting errors that could result in penalties.
Attendance
Traditional manual process methods for time and attendance don’t give your employees the flexibility and efficiency they often need to be productive. During a study, the participants were asked how their break times and lunch breaks were recorded. 45% revealed that they had to manually enter their breaks and lunches on paper time cards.
Working within a manufacturing environment, you need the speed and accuracy to consistently produce. Manually entering attendance can only lead to inaccuracies.
In our survey, 47% of the participants revealed that attendance was one of the biggest bottlenecks within their warehouse.
Enforcing your organizations attendance policy can be tedious and time consuming. 18% of the participants revealed that they did not know or understand their manufacturing company’s attendance policy, and an additional 16% stated they only somewhat understood it. Advanced time and attendance software can improve workforce management and ensure your company policies are being implemented automatically as attendance issues arise.
Our study revealed that 38% of the participants felt that scheduling was one of the main administrative procedures that needed to be improved on within the warehouse, while 25% stated it was employee absences and tardiness. Having a fully-integrated system, to automatically track and schedule employees in real-time, can cut your administrative burden in half.
Reduce your organization’s costs and administrative workload with an effective attendance program.